Don’t force a square peg into a round hole
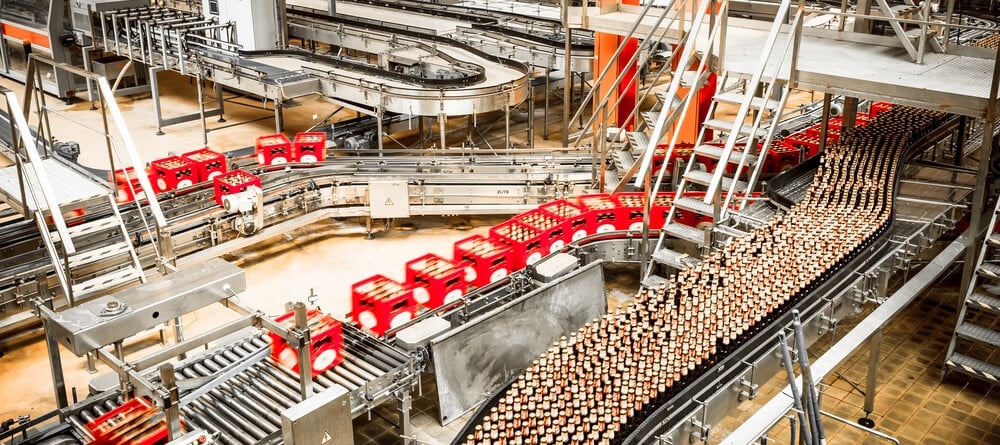
The Apollo 13 movie air scrubber repair scene is dramatic. Lives were at stake and the clock was ticking for a team of engineers to come up with an ad hoc air scrubber using only the parts on hand. The air scrubber repair was good enough for Apollo 13 to limp home. Ultimately, the team saved the astronauts’ lives and the nation’s prestige. This was a true story of derring-do and makes for great cinema.
The case for using whatever parts are on hand to make repairs in the world of manufacturing may not be as dramatic. However, maintenance people are under significant pressure to maintain uptime. Downtime means loss of production, revenue, profit, and even trust. When the pressure is on, maintenance teams can be quite skilled in cobbling together a repair solution on the fly with the parts on hand in inventory to get systems up and running again.
In solving an immediate maintenance problem to get a production line back up, it’s easy to create hidden risk by focusing only on raw uptime - especially in industries like food manufacturing – without also focusing on making a Hazard Analysis Risk-based Preventative Controls (HARPC)-compliant repair with the right part.
Examples of when close is not good enough
Without an accurate, up-to-date and well-documented maintenance inventory, including HARPC-compliant functional equivalent parts, maintenance staff either won’t know the risks or will be tempted to accept dangerous risk in selecting an ad hoc replacement part. A system that minimizes breakdowns, also minimizes HARPC- related risks, especially during start up and shut down. Here are some real-world examples.
Example: Maintenance replaced a stainless steel mechanical water tank float with a brass mechanical water tank float. The chemicals in the water attacked the brass and put residual material into the water stream, and into the product. The parts and work order system gave no warning of a material concern or indication to perform a HARPC analysis on the new part. Water can contain chemicals benign to people, but have unforeseen reactions with equipment in a manufacturing process. These chemicals may not be known to food manufacturers, which is why HARPC is so important, and why replacement parts control is so important. Issues can become global very quickly.
Example: Maintenance replaced a failed ball valve with a slightly different part from maintenance inventory because the exact size was not in stock. The replacement was smaller than the original but the repair team added reducers to both sides of the smaller ball valve to make the repair water tight. The smaller ball valve became a choke point, lowering the volume of hot water circulating the system. During the initial system startup, the critical product “kill step” intended to generate heat to remove bacteria or condensate had too much temperature variation. This created an even more expensive failure as bacteria levels increased over a few days. To avoid possible food contamination, maintenance had to disassemble the entire system and sanitize it after the rebuild. This added unbudgeted additional operating cost. This also increased unplanned stress to the other production lines as they were used to produce more.
Example: A manufacturer had a requirement for a hammermill hammer that operated in one direction and provided about 4500 hours of service before replacement. A hammermill shreds or crushes aggregate material into smaller pieces by the repeated blows of little hammers. These machines have all sorts of applications in many industries, including ethanol plants and grain mills. The reliability team worked with a series of vendors to develop a two-month part reorder process with a six-month lead time. These specific hammers eliminated the need to reverse the hammermills every two weeks to ensure even wear, and to change hammers every six weeks. The manufacturer avoided significant downtime as a result. A new buyer who did not have the benefit of a detailed and accurate maintenance inventory database, noticed the custom hammers cost five times more than off-the-shelf equivalents. Without informing the reliability team, the buyer began ordering off-the-shelf hammers and stopped ordering the custom hammers that the PM and HARPC program had developed. At week eight of operations, an off-the-shelf hammer broke at the connecting point, shot through the outer casing of the hammermill and triggered the explosion suppression system. Five entire milling lines shut down with the actuation of the explosion suppression system. This caused twenty-eight hours of downtime on all milling lines, kicked of a costly and detailed investigation, and contaminated a lot of product. This cost far exceeded the more expensive custom, HARPC-compliant hammer.
Closed-Loop MRO Procurement for HARPC Compliancy
An accurate and near-real time maintenance inventory increases the probability that maintenance will have the part they need when they need it for repairs. An accurate and near-real time maintenance inventory requires tight integration between purchasing and a computerized maintenance management system / enterprise asset management (CMMS/EAM) parts inventory database.
Near-real time integration between purchasing and a CMMS/EAM parts inventory database sits at the heart of a Closed-Loop MRO Procurement solution, which is key to helping manufacturers maintain HARPC-compliant systems.
In Closed-Loop MRO Procurement, the procurement system monitors the CMMS/EAM in real time to determine when parts go below their re-order points. When this happens, the system creates an RFQ or Purchase Order and alerts the Procurement team that they need to make a purchase. When a Purchase Order is placed, the system automatically updates the Quantity on Order information in the CMMS/EAM. And when the order arrives, the system automatically decrements the Quantity on Order information and increments the Quantity on Hand information.
Closed-Loop MRO Procurement Benefits
A Closed-Loop MRO Procurement solution transforms a HARPC-compliance paper-exercise into real rubber-meets-the-road compliance in production environments. Closed-Loop MRO Procurement benefits also include:
- Fewer parts outages which results in higher uptime and more reliable assets & equipment
- Fewer emergency shipments, resulting in lower shipping costs
- Lower inventory levels, resulting in both lower depreciation expense and lower working capital utilization
- Lower purchase prices, resulting in a lower overall maintenance spend
- Lots of time saved and more accurate inventory information through the elimination of tedious, manual work
What is the impact of Closed-Loop MRO Procurement on the bottom line? Through a combination changes in people, process and tools, companies see a 25% reduction (or more) of maintenance-related purchases.
Clearly the automation of procurement in general and MRO procurement in particular can have a dramatic impact on the bottom line. The right procurement management system can be the secret sauce to enable Closed-Loop MRO.
Contact us to learn more about Closed-Loop MRO and what it can do for your profitability and efficiency.
JOIN OUR
MAILING LIST
RELATED POST
- Be a better buyer with Closed-Loop Maintenance, Repair, and Operations (MRO) Purchasing
- Contraqer Corp. Partners with Smartware Group to Enable Closed-Loop MRO Procurement
- Contraqer Successfully Deploys Closed-Loop MRO Procurement Solution at Grassland Dairy Products, Inc.
- Learn How Closed-Loop MRO Procurement Saves Time & Improves Uptime